Silicon Carbide Ceramic Foam Filter
Silicon Carbide Foam Filters are a modern day revolutionary filtration solution for the foundries that deal with gray iron, ductile iron, bronze, and other cast iron and non-ferrous alloys. These filters are crafted effectively to get rid of impurities, inclusion, and trapped gasses from the molten metal during the process of casting. Sic ceramic foam filters for casting from Cangzhou Sefu Ceramic New Materials Co., Ltd are highly porous and lightweight to play a vital role in improving the casting quality, reducing scrap rates, and to increase the overall profitability.
- Good porosity, no clogging when pouring molten metal.
- Mature production technology ensures good fire resistance and thermal shock resistance.
- Advanced cutting instruments precisely control size.
- Sufficient slurry, no breakage, and no filter residue.
Achieve Cleaner, Higher-Quality Castings with Silicon Carbide Ceramic Foam Filters
These silicon carbide foam filters are not just a normal one that you come across. They have a unique open cell structure that guides the molten metal to flow through as it captures the unwanted residues. As these molten metal filters refine the impurities and gas bubbles, they help the foundries to produce cleaner metals with fewer defects, leading to castings with improved mechanical properties, and a neat and smoother surface. These fundamental qualities of a top-notch casting work result in a longer life span of the product, ultimately exceeding the customers’ satisfaction.
- Performance Indicators
- Regular Sizes and Filtration Capacity
Chemical Composition | SiC, Al2O3, SiO2 |
Porosity(%) | 80~90% |
Application Temperature | Max.1500°C |
Color | Grey |
Bending Strength(Mpa) | 0.8 Compression |
Strength(Mpa) | 0.9 Thermal Shock |
Resistance | 1100°C (room temperature 6 times) |
Volume Density | 0.4-0.5g/cm3 |
Tolerance of Dimensions | -1.5∽0.5mm |
Size (mm) |
10ppi | 20ppi | 30ppi | |||||
Capacity (kg) |
Flow Rate (Kg/s) |
Capacity (kg) |
Flow Rate (kg/s) |
Capacity (kg) |
Flow Rate (kg/s) |
|||
Grey Iron | Ductile Iron | Grey Iron | Ductile Iron | Grey Iron |
Grey Iron |
Grey Iron | Grey Iron | |
40×40×15 | 64 | 32 | 4 | 3 | 50 | 3 | 42 | 2 |
40×40×22 | 64 | 32 | 4 | 3 | 50 | 3 | 42 | 2 |
50×30×22 | 60 | 30 | 4 | 3 | 47 | 3 | 40 | 2 |
50×50×15 | 100 | 50 | 6 | 4 | 78 | 3.5 | 66 | 3 |
50×50×22 | 100 | 50 | 6 | 4 | 78 | 3.5 | 66 | 3 |
60×60×15 | 144 | 72 | 9 | 6 | 112 | 6 | 95 | 5 |
75×50×22 | 150 | 75 | 9 | 6 | 116 | 6 | 99 | 5 |
75×75×22 | 220 | 110 | 14 | 9 | 175 | 10 | 149 | 8 |
100×50×22 | 200 | 100 | 12 | 8 | 155 | 9 | 133 | 7 |
100×75×22 | 300 | 150 | 18 | 12 | 232 | 13 | 199 | 11 |
100×100×22 | 400 | 200 | 24 | 16 | 310 | 18 | 265 | 15 |
150×150×22 | 900 | 450 | 54 | 36 | 698 | 40 | 596 | 33 |
200×200×40 | 1600 | 800 | 95 | 64 | 1240 | 58 | 1060 | 48 |
Dia 40×22 | 40 | 20 | 3 | 2 | 39 | 2 | 33 | 2 |
Dia 50×22 | 70 | 35 | 4.5 | 3 | 61 | 4 | 52 | 3 |
Dia 60×22 | 100 | 50 | 6.5 | 4.2 | 88 | 5 | 75 | 4 |
Dia 70×22 | 150 | 75 | 8.8 | 5.5 | 119 | 7 | 102 | 6 |
Dia 75×22 | 170 | 88 | 10 | 6 | 137 | 8 | 117 | 6.5 |
Dia 80×22 | 200 | 100 | 11 | 7.2 | 156 | 9 | 133 | 7 |
Dia 90×22 | 240 | 120 | 14 | 9 | 197 | 11 | 169 | 9 |
Dia 100×22 | 280 | 140 | 17 | 11 | 243 | 14 | 208 | 12 |
Dia 125×22 | 400 | 220 | 24 | 16 | 380 | 22 | 325 | 18 |
Dia 150×22 | 700 | 350 | 38 | 25 | 548 | 32 | 468 | 26 |
Dia 200×40 | 1240 | 620 | 67 | 44 | 973 | 56 | 832 | 46 |
Application of Silicon Ceramic Foam Filters
Sic filters are used to filter molten metal in the manufacture of ductile iron, grey iron, and bronze castings, as well as castings made of bronze, copper, and other non-ferrous alloy materials. Here are some most common applications for these filters:
- Automotive and Aerospace: In the demanding worlds of automotive and aerospace, these silicon foam filters ensure cleaner, lighter, and stronger engine blocks. Also they help to build the transmission housings, aircraft structures in regards to the aerospace industry.
- Hydraulic Components and Pump Valves: In the case of hydraulic components and pump valves, cleaner castings are essential for high pressure operation. Silicon Carbide Foam Filters address this by filtering out inclusions that could weaken the structure, leading to improved performance, and extended service life.
- Wind Turbines and Machine Tools: Wind turbines and machine tools both require durability, and precision. Filtering of molten metal used in various components, results in cleaner microstructures with enhanced wear resistance and dimensional stability. This filtration by silicon foam filter ultimately contributes to reliable and efficient operation in both wind power generation and high-precision machining.
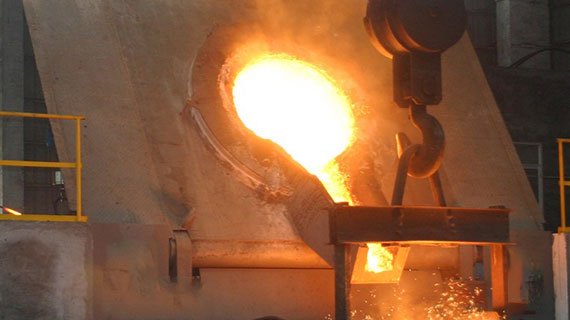
Unveiling the Power of Silicon Carbide Ceramic Foam Filters: A Feature Breakdown
Silicon ceramic filters are the game changer in the world of metal castings. They offer a different form of casting material from the molten metal. Here’s a closer look at the features of this powerhouse:
Reduced Rate of Rejections:
Sic foam filters with highly porous structures act as a meticulous barrier to the molten metal that flows through with a trail of impurities and inclusions. Also, this reliable ceramic filter for foundry features a strong absorption function that attracts and arrests the fine impurities to prevent them from becoming defects in the final casting. This exceptional filtration method drastically reduces the rejection rate and ensures consistent high quality castings.
Laminar Flow for Even Filling:
During casting, higher turbulence in the molten metal can cause uneven filling in the mold cavity. Silicon foam filters effortlessly eliminate this issue by promoting the laminar flow. Laminar flow optimizes and controls the flow of the molten metal to ensure the even filling with a more uniformed structure in the mold. This helps the final casting to possess a specific design and predictable mechanical properties as it cuts out the inconsistencies and defects from the flow of molten metal.
Aiding Processability and Enhancing Casting Strength:
Key features of these foundry ceramic filters don’t stop with just cleaner metals but they contribute to improving the casting processability. With fewer inclusion of impurities and a more uniformed structure, the cleaner metal achieved through the scrutinized filtration process allows the creation of casting with enhanced mechanical properties to boast the rigidness of the casting.
Revolutionize Casting with SiC Filters from Cangzhou Sefu
In the quest for high quality castings, look no further than Cangzhou Sefu Ceramic New Materials Co., Ltd. Being a leading manufacturer we offer exceptional Silicon Ceramic Foam Filters which are crafted to revolutionize your casting process. At Cangzhou Sefu, we prioritize innovation and quality. Hence, our filters are manufactured using top-grade materials and our rigorous quality control process ensures consistent performance and reliability of these filters. As we understand the diverse needs of various casting applications, we offer customization options for our Sic foam filters. Our team of experts can also provide technical guidance to help you select the optimal filter for your needs.

Related Products
SEFU team supplies you with more molten metal filtration products and other foundry materials to help you improve casting quality and save production costs.
FAQ Guide About Silicon Carbide Ceramic Foam Filters
Do you have more information about Silicon Carbide Ceramic Foam Filters? This FAQ section can help you learn more.
If you want to know anything else about ceramic foam filters, please contact us to leave your questions, professional foundry solutions are waiting for you.
SiC ceramic foam filters are used to filter impurities and inclusions from molten metal during the casting process. They are particularly effective for cast iron, bronze, and other non-ferrous alloys.
No, SiC ceramic foam filters are single-use consumables. The captured impurities render them unusable for subsequent casting processes.
While there’s an initial investment in the filters, they can significantly reduce scrap rates and improve process efficiency. This translates to overall cost savings in the long run.
By minimizing casting rejects, SiC ceramic foam filters contribute to a more sustainable casting operation by reducing the need for re-melting scrap metal.
Visit our website or contact our sales team for detailed specifications, technical guidance, and a quote for your specific casting needs.