Alumina Ceramic Foam Filter
Any project involving the casting of aluminum depends on the quality of the molten metal. The integrity, functionality, and appearance of the finished product can all be seriously harmed by inclusions, contaminants, and trapped gases. Alumina ceramic foam filters, sometimes referred to as ceramic filters for foundries or aluminum casting filters, provide a dependable and effective way to produce cleaner aluminum castings.
- Superior dimensional tolerances.
- Stable in the chemical property.
- Improve microstructure
- Excellent filtration efficiency.
- Good in mechanical strength.
- Resistant to corrosion and thermal shock
- Porosity, Performance Specifications, and Customization
Alumina ceramic foam filters come in a range of porosities, measured in pores per inch (PPI). Higher PPI filters offer enhanced filtration efficiency for capturing finer particles, while lower PPI options prioritize faster flow rates.
Here’s a quick overview of the typical performance specifications of alumina ceramic foam filters:
- Porosity: 80% ~ 90%
- Working Temperature: ≤ 1200°C (2192°F)
- Volume Density: ≤ 0.5 g/cm³
- Compression Strength (Room Temperature): ≥ 1.0 MPa (145 psi)
- Thermal Shock Resistance: 800°C to room temperature, 5 cycles
Ceramic filter for casting manufacturers can also provide customized filter sizes and shapes to accommodate specific casting applications.
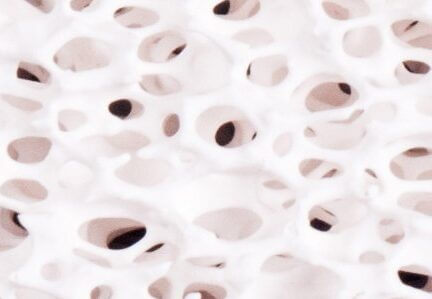
Applications of Alumina Ceramic Foam Filters
Many different aluminum casting applications use alumina ceramic foam filters, such as:
- Aluminum profile production: These filters guarantee the structural integrity and smooth surface finish needed for extruded items such as window frames and architectural profiles.
- Aluminum foil production: Alumina ceramic foam filters are good at removing contaminants that uniform the thickness and produce high-quality optimal heat for food packaging.
- Aluminum alloy casting: Aluminum casting filters ensure minimal casting flaws and a cleaner metal flow during the production of engine blocks, wheels, and other intricate components.
Manufacturers of ceramic foam filters also provide versions that are appropriate for filtering other molten metals, like bronze and magnesium, in addition to aluminum.
Advantages of Alumina Ceramic Foam Filters
There are several benefits that alumina ceramic foam filters offer over conventional filtration techniques.
- Superior Filtration Efficiency: The highly porous structure of these filters’ efficiently eliminates big inclusions and catches micron-sized particles that result in much cleaner molten metals,
- Better Casting Quality: Improved mechanical characteristics and smooth surface finish in the final casting are easily achieved with the help of these Alumina ceramic foam filters as they provide a finer microstructure by removing impurities and trapped gases.
- Increased Yield Rate: Reduced casting flaws result in a greater yield rate of useable castings, which reduces waste during production and maximizes resource use.
- Production Process Simplified: These alumina ceramic foam filters feature a plug-and-play setup and have quick integration into the current foundry operations which helps you speed up the production cycle.
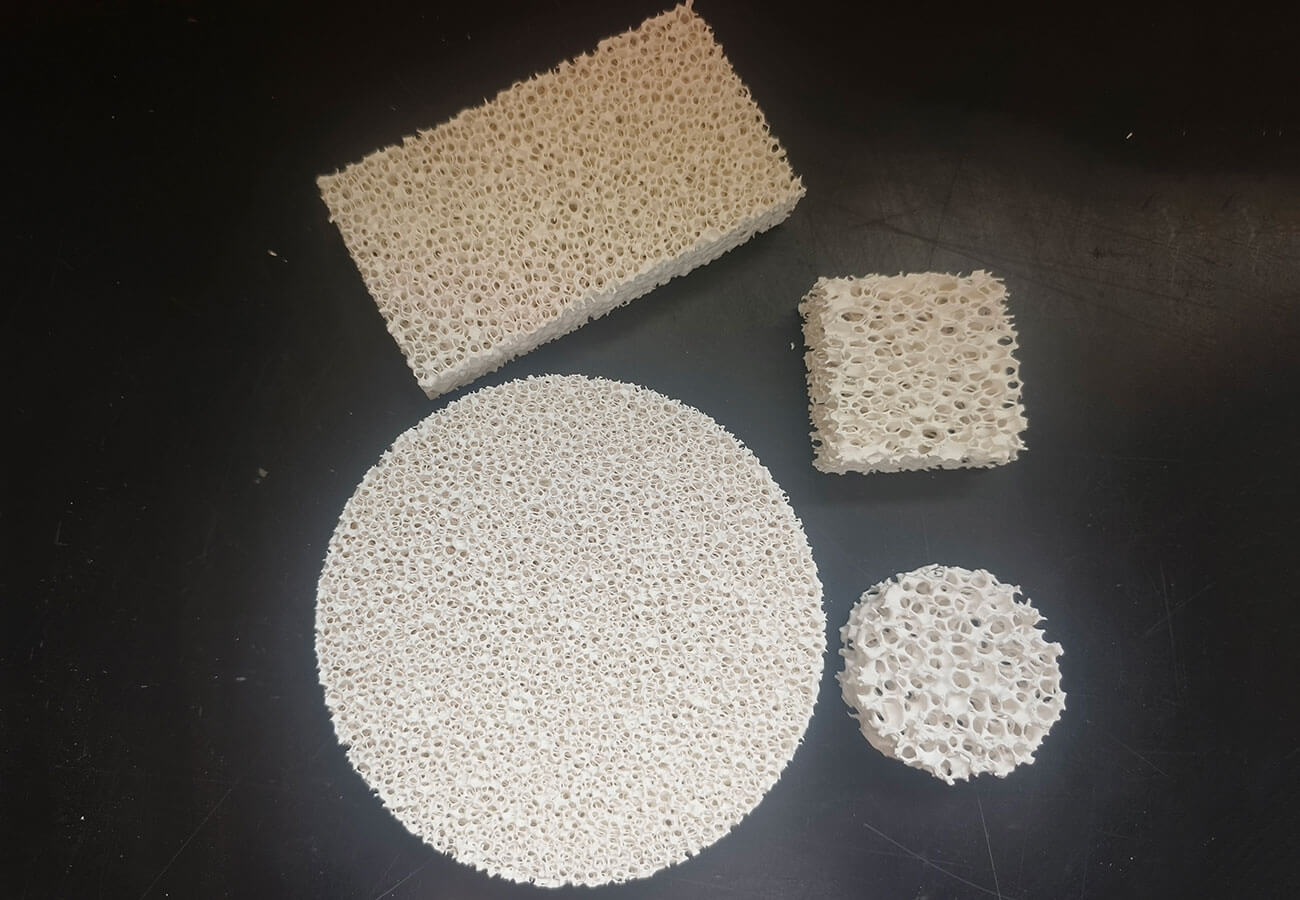
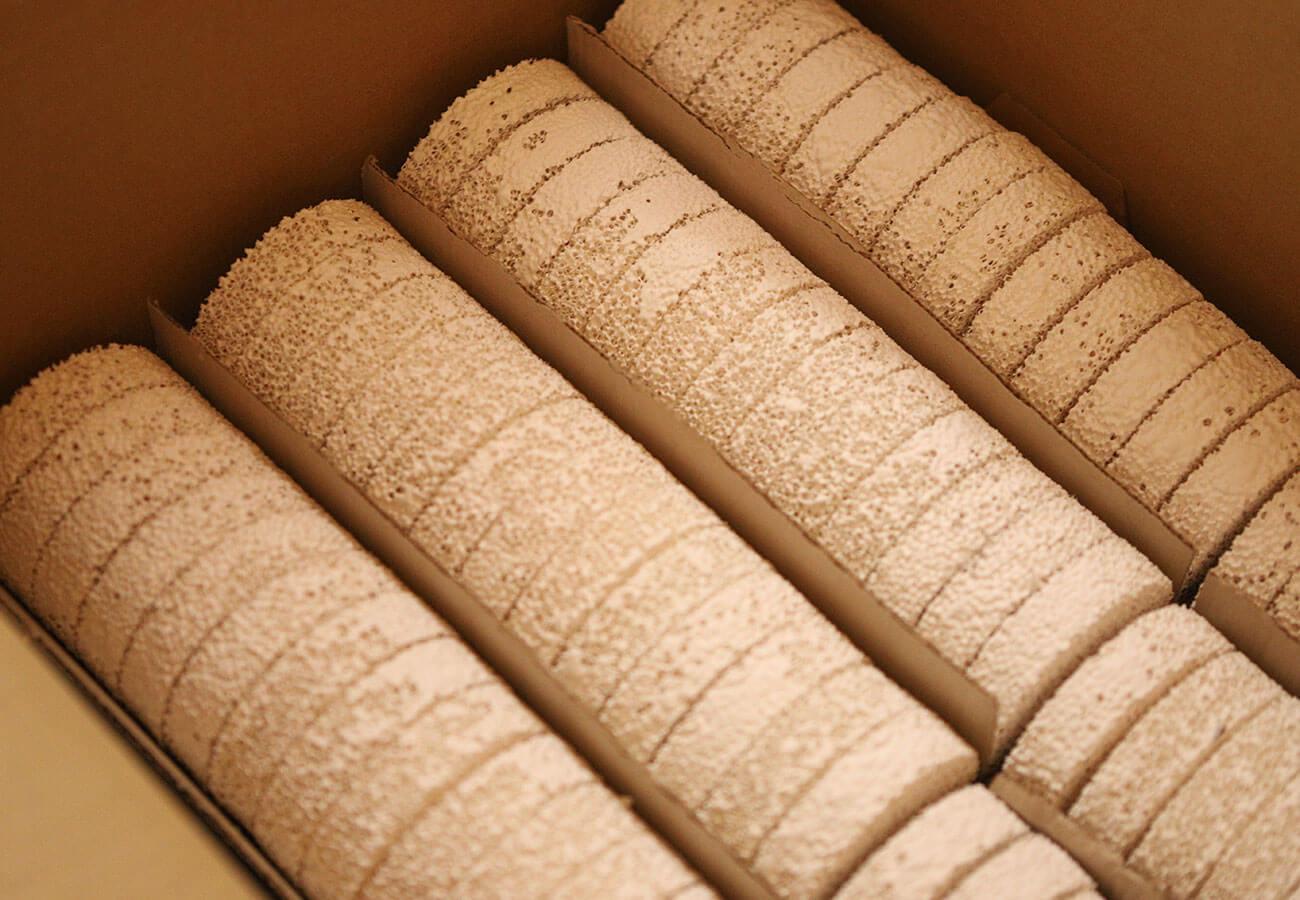
Features of Alumina Ceramic Foam Filters
The exquisite craftsmanship of alumina ceramic foam filters results in remarkable performance:
- Accurate Dimensional Tolerances: Our filters are made with strict tolerances in order to avoid bypasses and preserve constant filtration, and also to guarantee a precise fit inside the filter box.
- Stable Chemical Properties: These filters possess exceptional chemical resistance to molten aluminum as they are made out of high-purity alumina (aluminum oxide). This feature keeps the filter clean and intact during the casting process.
- Superior Mechanical Strength: Despite the porous nature of the Alumina ceramic foam filters, they have exceptional mechanical strength, that enables them to endure the pressure and heat requirements of molten metal casting.
- Thermal Shock Resistance: These filters guarantee a dependable operation in conditions with high temperatures used in foundries as they are crafted to withstand sharp temperature changes without breaking down or deteriorating.
- Beveled Edges and Compressible Gasket: Efficient filtration and reduced leakage is ensured by the compressible gaskets and beveled edges by creating a tight seal inside the filter box.
Quality & Service: Delivering Value to Our Customers
At Cangzhou Sefu Ceramic New Materials Co. Ltd., we are aware of how important alumina ceramic foam filters are to producing aluminum castings of the highest caliber. For this reason, we’re dedicated to offering:
- Excellent Quality Products: Our filters are made out of premium raw materials and subjected to stringent quality control procedures to guarantee seamless performance and high dependability.
- Technical expertise: Our team of seasoned experts will guide you to choose the best foam filters according to your custom requirements through a grasp of aluminum casting processes
- Superb Customer Service: To guarantee your success in producing cleaner and higher-quality castings, we are committed to providing prompt assistance and thorough technical coaching.
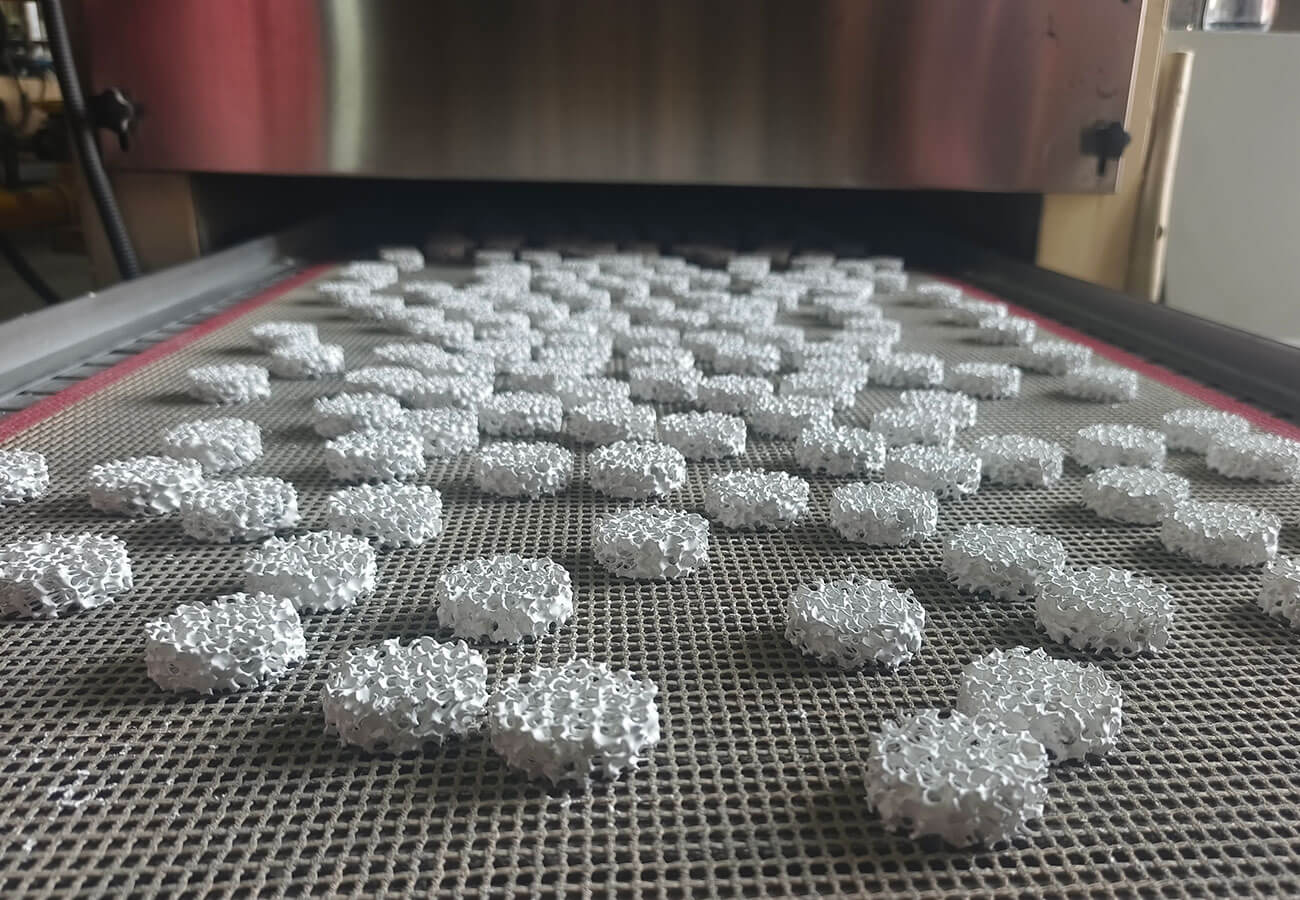
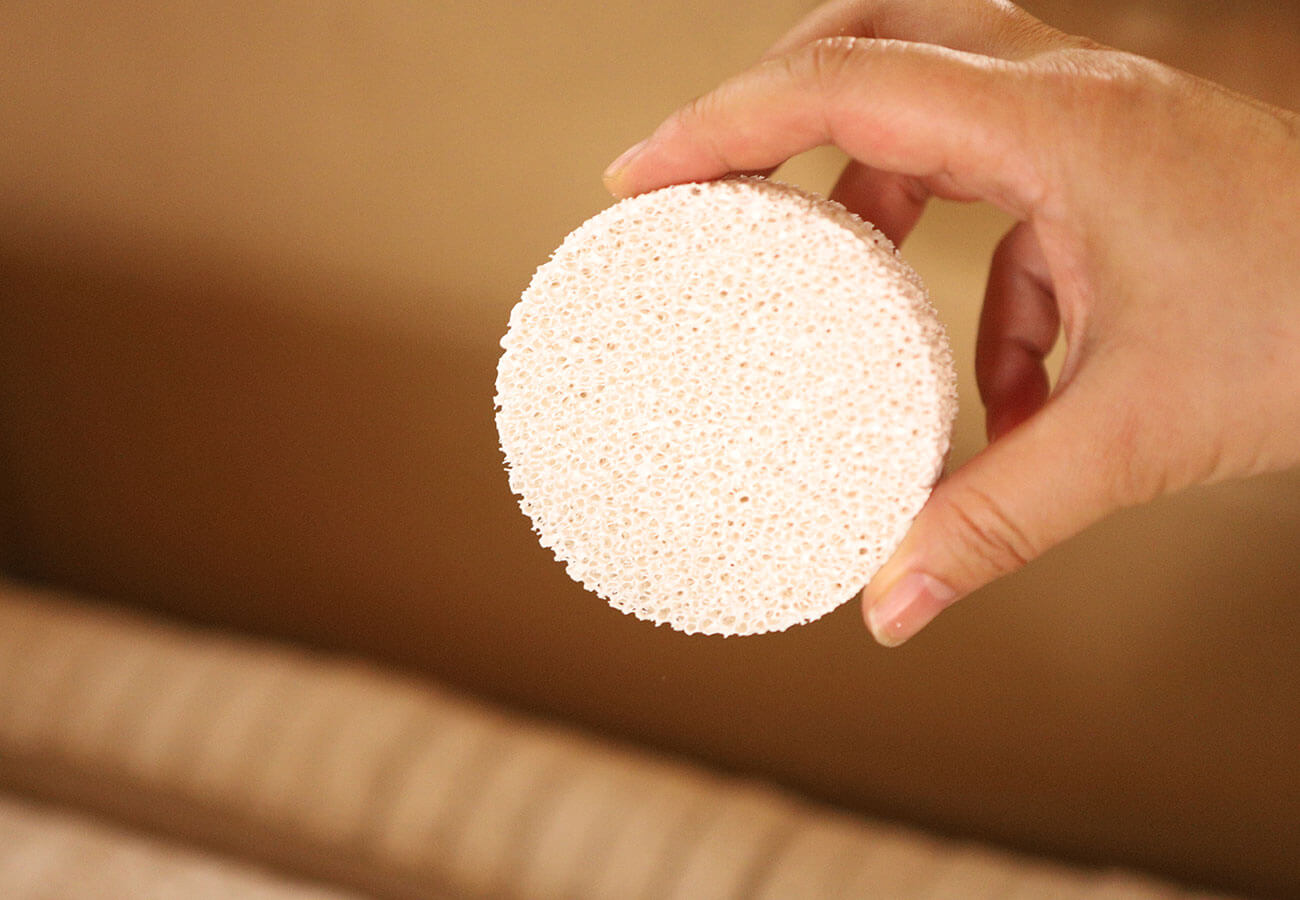
Achieve Peak Performance with Alumina Ceramic Foam Filters
By incorporating alumina ceramic foam filters into your aluminum casting process, you can unlock a multitude of benefits. From achieving superior casting quality and increased yield rates to streamlined production processes and enhanced profitability, these versatile filters are an investment in success.
Contact Cangzhou Sefu New Materials Co,. Ltd. today to discuss your specific aluminum casting requirements and explore how our high-performance alumina ceramic foam filters can elevate your operations to new heights. We are confident that we can provide the filtration solutions you need to achieve cleaner, higher-quality castings consistently.
Remember:
- Always preheat alumina ceramic foam filters before use according to the manufacturer’s instructions.
- Consider contacting your chosen foundry ceramic filter manufacturer for specific guidance on filter selection and preheating procedures.
Choose Cangzhou Sefu New Materials Co. Ltd. as your trusted partner for premium alumina ceramic foam filters and experience the difference exceptional quality and expert support can make in your aluminum casting endeavors.
Frequently Asked Questions (FAQ) about Alumina Ceramic Foam Filters
What else would you like to know about Alumina Ceramic Foam Filters? Leave your questions and let our experienced engineers help you.
Choosing the right PPI depends on your application’s balance between filtration and flow rate. Higher PPI filters capture finer particles for cleaner metal, while lower PPI options prioritize flow rate. Consult a reputable manufacturer or their specifications to find the optimal PPI for your needs.
Proper preheating is crucial to prevent thermal shock and ensure optimal filter performance. Gradual heating at a controlled rate is recommended, following the specific guidelines provided by your chosen ceramic filter for foundry manufacturer.
While alumina ceramic foam filters are designed for single use in the foundry, some manufacturers offer reusability options under specific conditions. However, for optimal performance and to ensure consistent filtration efficiency, it’s generally recommended to use a fresh filter for each casting process.
Alternative molten metal filtration options include mesh filters. However, alumina ceramic foam filters offer several advantages, including superior filtration efficiency, higher mechanical strength, and improved thermal shock resistance.
Reputable manufacturers prioritize quality control and offer a wide range of filter options to suit diverse casting applications. Look for manufacturers with a proven track record and a commitment to customer service. SEFU CERAMIC has many years of experience in production and global supply. The product quality and service are guaranteed. Please feel free to contact us through the form on the right.