Antioxidant Graphite Rotor for Aluminum Alloy Smelting
Improve the purity of aluminum and alloys with SEFU’s graphite degassing rotors. Designed for smelting operations, they enhance gas distribution, efficiently removing hydrogen and other impurities.
- High strength
- High purity
- High density
- High temperature resistance
- Corrosion resistance
- Antioxidant
- Customizable
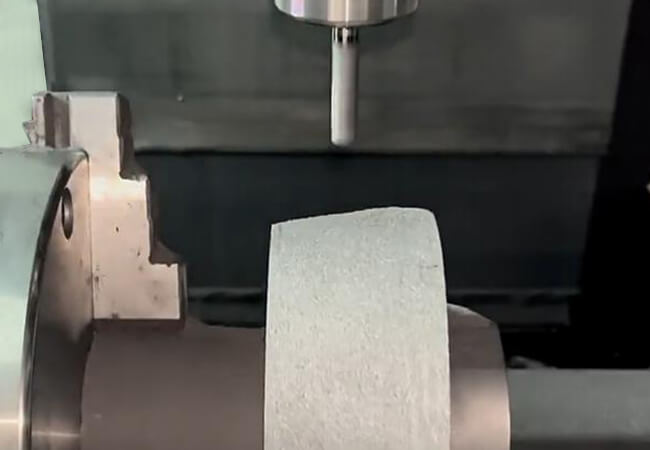
Description
SEFU’s graphite rotors consist of a high-quality isostatic graphite rod coupled with a round-shaped impeller. They are manufactured from fine-grain graphite to offer excellent thermal conductivity, heat resistance, and non-reactivity with molten aluminum. The degassing rotor is designed with a threaded coupling system for quick assembly and disassembly, as well as to offer better stability under high-speed operations.
Why Our Graphite Rotor Assemblies For Your Smelting Operations
Cangzhou Sefu Ceramic New Materials Co., Ltd specializes in designing graphite products tailored for aluminum and alloy production. In the degassing and purification of aluminum liquid in foundries, all graphite rotor assemblies’ geometries differ depending on the treatment vessel. To keep up with dimensional precision, SEFU conducts numerous studies and simulation practices.
We’re here to make your smelting operation smoother with our graphite rotor assemblies, which help greatly reduce machining costs for repeated use.
Looking for personalized graphite rotor assemblies for your smelting operations?
SEFU is here to assist you every step of the way. You can leverage our customized manufacturing services. Our experts will guide you through all the technical details you need. Contact us to get more details!

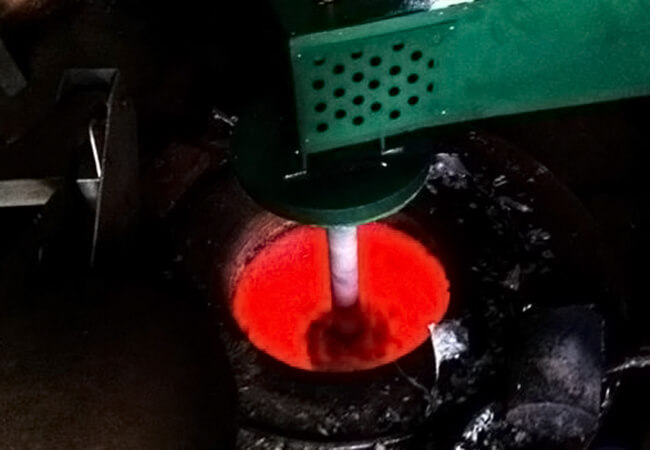
Benefits Of Our Degassing Rotor
- Reduction in Thermal Stress Failures: Stable at high temperatures. Uniform in mixing and gas dispersion.
- Minimizing Gas and Impurity Infiltration: Designed with high-density graphite to reduce deformation and erosion.
- Resistant to Corrosion and Oxidation: Treated with antioxidants. Neither acidic nor alkaline conditions can force degradation.
- Less Vibration During Operations: Precisely designed rods and shafts neglect vibrations during motions.
- Quick Change-Out Capability: The thread lock system gives a quick and easy replacement.
Developing High-Quality Graphite Products
SEFU is fully integrated. Graphite products manufactured in our ISO-certified facility, are dimensionally intact. They are fit and free of structural intolerances. These shafts and rotors are applied with antioxidation coatings, offering better machinability in high-temperature applications
- They produce smaller purge gas bubbles.
- They uniformly disperse the gas bubbles throughout the melt volume, ensuring no weak points are created.
- They provide fuller mixing as no dead zones are formed, leading to better melt circulation.
- They reduce the surface agitation of the melt. This lowers the possibility of oxidation and the formation of other contaminants.
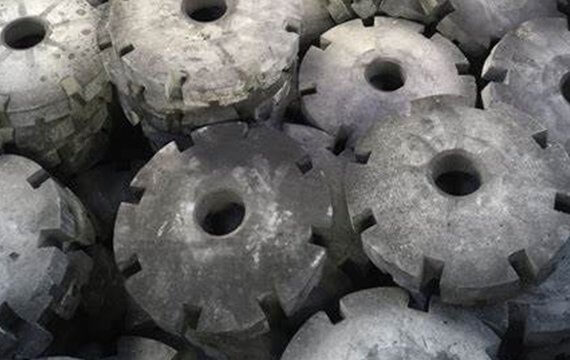
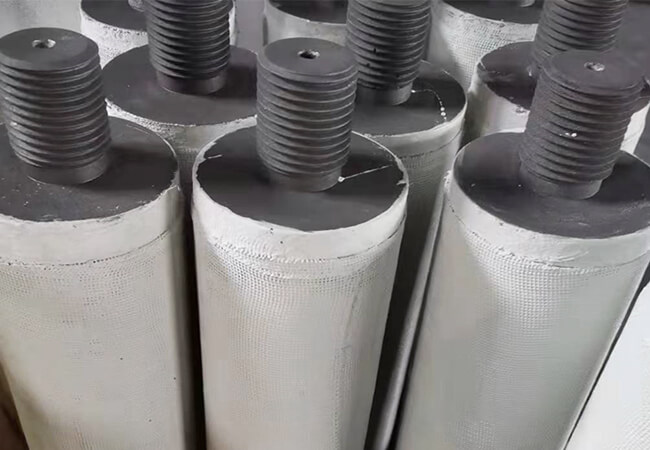
Industries Served In
Uniform surface quality, lightweight properties, and high purity are essential requirements in the production of aluminum foils, plates, alloy wheels, and other products. Our optimized degassing rotors are designed to minimize gas porosity by efficiently removing dissolved hydrogen from molten aluminum.The degassed aluminum contributes in various ways across industries:
- Automotive: Engine blocks, cylinder heads, wheels, and body panels for ensuring lightweight for better fuel efficiency
- Aerospace: Aircraft engines and braking systems to reduce porosity
- Power Generation: turbines, compressors, heat exchangers, where the degassed aluminum improves longevity and energy efficiency.
Before setting up the rotor onto the shaft, make sure it is free of grease, dirt, or other contaminants. It comes with a DSK-type screw coupling system. Thread the rotor onto the shaft and tighten it. Before dipping it into the mold, do a test rotation at low speed and confirm that there is no wobbling during the rotation.
For aluminum, nitrogen or argon have been technically tested and proven. Since they don’t react with each other, they can effectively remove impurities. Nitrogen is also a crucial inert gas for copper and its alloys, while argon works well for magnesium and stainless steel. When choosing a gas to purify metals with a rotor degasser, consider both the metal’s properties and the impurities you want to remove.
Graphite rotors improve degassing efficiency by removing hydrogen and other impurities trapped in aluminum liquids through the distribution of inert gases. These rotors use the impeller principle to break the gases into tiny bubbles, which latch onto impurities and clean the melt.
Yes, it does, though graphite naturally has better thermal stability and retains its mechanical properties at high temperatures. Sefu has impregnated anti-oxidation coatings into the rotor to withstand oxygen-rich environments.
When designing our graphite products, we consider various factors, both in design and material choice, that control the uniform gas dispersion throughout the aluminum liquid. These factors include:
- Precision blade design shapes
- Rotational speed balance
- Thermal stability of the graphite
- Controlled bubble formation
Though degassing is the primary purpose of graphite rotors, they are used in many other ways as well. They are used for purifying liquid aluminum, removing slag, blowing, and homogenizing molten aluminum.
To provide you with an accurate quotation, please share the material dimensions (thickness, width, and length). If you have technical drawings or schematic references, kindly attach them to the file, along with mechanical and technical details such as surface conditions, strength, hardness, and thermal properties, as well as the required order volume.