Aluminum Casting: Molten Metal Auto Pouring Ladles
SEFU Molten Metal Auto Pouring Ladles are containers used to transfer aluminum liquid during the aluminum refining process. It is installed on the automatic pouring device and transfers the molten metal from the holding furnace to the pouring cup.
- Lightweight materials
- Can be started cold, no preheating required
- Very good wear resistance and thermal insulation
- Low heat and temperature dissipation
- Superior mechanical properties
- Special strength and density ratio, density is 1600Kg/m3
- Does not stick to molten aluminum
- Not stained by iron impurities
- Low maintenance cost
- Technical Parameters
- SEFU Certification
Can be processed according to your needs
- Product specifications: 0.5-120kg
- Density: 1600 Kg/m3
- Maximum operating temperature: 780℃
- Thickness: 8-25mm
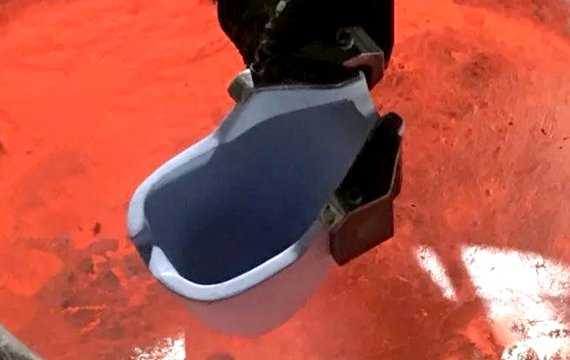
Molten Metal Auto Pouring Ladles, fiber-ceramic composite pouring ladles, are containers installed on automatic pouring devices to transfer molten aluminum.
Fiber-ceramic composite materials are made of fiber-based ceramic materials as binders, which are laminated and compounded. They are tough and resistant to mild mechanical damage.
When it leaves the factory, its surface is all painted with special paint. The special non-stick properties of this paint enhance the performance of the fiber-ceramic composite automatic ladle.
How to use fiber ceramic composite automatic ladle?
Fiber ceramic composite pouring spoons can be used in high-pressure casting, gravity casting, and sand casting.
The SEFU fiber ceramic composite auto pouring spoon is designed to meet the needs of most customers and is connected with a special connecting block and robotic arm. The pouring ladle is fixed by tightening the bolts, and slight size differences can be perfectly matched by grinding or filling with refractory mud.
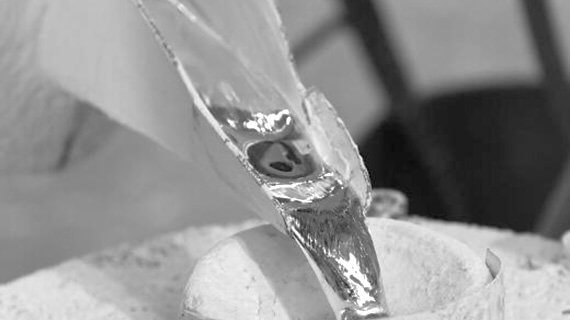

Features of SEFU Auto Pouring Ladle
- Lightweight: The cross-section of the sides and base of the ladle is much thinner and lighter than ordinary refractory materials.
- Excellent Thermal Insulation: The fiber-based composite material has a laminated structure that makes it difficult for heat to be conducted out, so its thermal insulation performance is very good.
- High Density: Good strength and density ratio, material density of 1600kg/m3.
- Non-stick Aluminum: The automatic pouring spoon is sprayed with a special coating when it leaves the factory. This coating has very good non-stick properties to aluminum.
- Safe & Reliable: Its service life is usually more than 40,000 castings
Advantages of SEFU fiber ceramic composite ladle
Different from vacuum formed ceramic fiber spoons using aluminum silicate fiber cotton, fiber-ceramic composite spoons are made by laminating fiber mesh cloth and ceramic mud. It is formed by laminating high silica fiber and refractory mud materials. These layered materials have good strength, toughness, safety, and stability. Moreover, the laminated structure of the fiber material makes it difficult for heat to be conducted out, so it has very good thermal insulation properties.
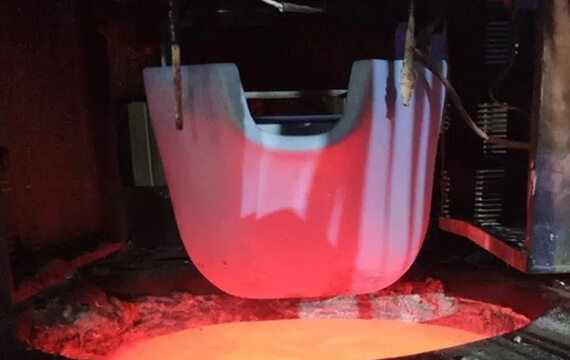
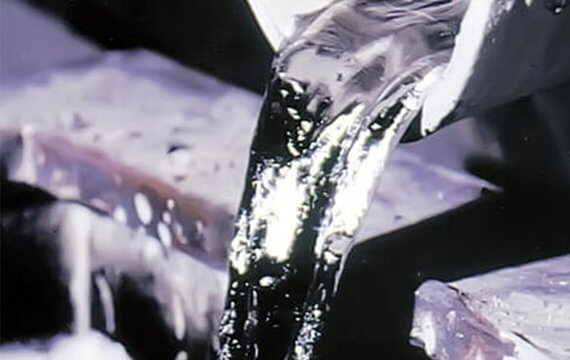
Why choose SEFU CERAMIC?
SEFU CERAMIC is committed to the development and production of thermal insulation products, refractory materials, and metallurgical materials.
We have introduced automated production equipment and production lines, and cooperated with many aluminum equipment companies around the world, specializing in customizing various refractory materials and various thermal insulation products that come into contact with liquid aluminum, such as filtering and degassing equipment, and liquid aluminum transfer tools. Such as pouring ladles, etc.
Note:
- Adjusting the pouring angle to pour out the aluminum liquid completely is recommended.(During the use of the pouring spoon, the residual aluminum liquid in the pouring spoon will solidify due to not pouring out completely, which will cause the solidified aluminum to expand in volume and cause cracks at the bottom when it is used again.)
- Excessive preheating, preheating at too high a temperature, and preheating for too long will reduce the service life of the ladle and may even cause it to break.